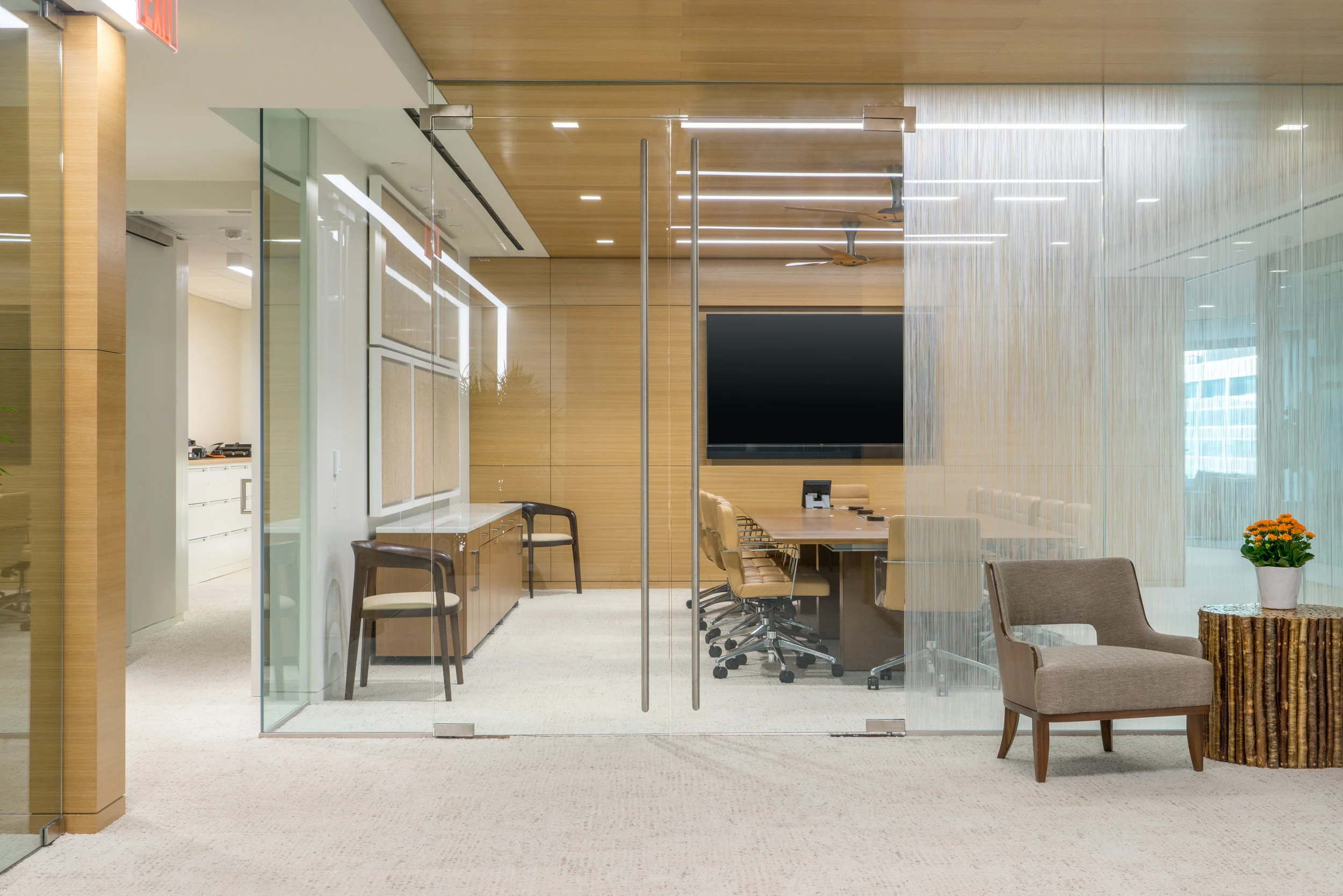
Credits
The project is rated LEED v4 ID+C, Platinum. More information about this rating system can be found on the USGBC's webpage.
Location + Transportation
The project is located in a 12-story, 386,000 square foot LEED Platinum Building completed in 2012.
Access to Quality Transit
The site is in the Washington, D.C. city center and easily accessible by bike or public transit. It is one block from the Farragut West Metro Station and across the street from Farragut North Metro Station.
Bicycle Facilities
There is an on-site fitness center with showers and locker rooms. Bike parking is located in the basement parking garage.
The base building water fixtures are designed to achieve water savings of 40% over the LEED baseline.
WATER EFFICIENCY
The Summit Foundation space included water use only in the kitchen area. The percent reduction for these fixtures from the baseline (before alternative water sources) is 55%.
LEED Water Efficiency Calculator.
To achieve the water savings, a combination of very low-flow fixtures and a Neoperl Cache 1.0 gpm faucet aerator were used.
Water Efficiency
Energy efficiency was a key priority for the design. Although this tenant improvement space was not a candidate for renewable energy, it was able to reduce its energy use considerably with efficient lighting, plug load monitoring, EneryStar appliances, and efficient mechanical systems.
Commissioning
Commissioning was performed to ensure that the built systems were operating per the Basis of Design and Owner's Project Requirements and that no energy was wasted through operational errors. The summary of commissioning activities can be found here.
For more information on commissioning see this article.
OPTIMIZE ENERGY PERFORMANCE
The office reduced its energy use (per the LEED baseline, ASHRAE 90.1-2010) by 24% through efficient equipment, reduced plug loads, high-tech lighting, daylight harvesting, energy star appliances, and a focus on thermal comfort. The energy model was performed using EnergyPro. The energy source is 100% electric. LED lighting was used to improve lighting efficiency by 55%.
Learn more about LED lighting.
Savings of up to 38% were seen for cooling due in part to Therma Fuser VAV Diffuser Controls.
The team performed a Net Zero Energy (NZE) study to see if 100% of the energy used by the Summit Foundation could be offset on-site. With extensive gardens on the roof it was hard to find space for solar panels, however, the project can upgrade the base building lighting to completely offset their own energy use.
Learn more about NZE Certification.
Energy Metering
The project pursued the LEED Credit Option 1:
"The project has permanently-installed, tenant-level energy meters that account for all sources of energy delivered to the project and represent total tenant energy consumption."
GREEN POWER
Green Power (renewable energy credit) was purchased through 3Degrees. 37 MtCO2e was offset through the McKinney Landfill Gas Methane Capture Offset Project in Dallas, Texas (shown below). These are Green-e Certified carbon offsets.
Energy and Atmosphere
Materials and Resources
Since the project set a goal to achieve the Living Building Challenge Materials Petal, the team also put a heavy emphasis on the LEED Materials and Resources credits.
Construction Waste Management
95% of construction waste was diverted from landfills through recycling, composting, take-back programs, and salvage donations. See the Construction Waste Management Plan that guided the process here.
Long-Term Commitment
The Summit Foundation signed a 10-year lease which will help to reduce waste from construction demolition over short tenant life-cycles.
Building Product Disclosure and Optimization
A number of resources for product selection were used, including the product lists from Living Building Case Studies and a combination of the following databases: Declare, UL, Pharos, and ARCOM (formerly Green Wizard). Nearly all products were transparent about 100% of their material ingredients.
22% of products (from 5 different manufacturers) used had raw material source extraction reports.
- 100% of wood products had vendor Chain of Custody certificate numbers with FSC certification.
- Salvaged materials included wood doors (pictured below).
- The total recycled content was 72% by cost.
The sustainable criteria value as a percentage of total materials cost was 30%.
- 4 products were Cradle-to-Cradle certified.
- 11 products had Health Product Declarations.
- 16 products had Environmental Product Declarations.
Health, air quality, daylight and views were key components of the design.
Minimum indoor air quality performance
The systems were designed to meet the required outdoor flow rates of ASHRAE Standard 62.1-2010. The spaces are ventilated by a base-building AHU. VAV boxes serve each zone in the project space. Each zone is sub-zoned with VAV diffusers with minimum ventilation set-points.
Low-Emitting Materials
The project used the LEED budget calculation method to achieve 75% compliance with the CDPH SM V1.1-2010, Section 8 guideline for all products, including furniture.
Indoor air quality assessment
Both a flush-out and air testing (see report here) were performed to ensure exceptional indoor air quality. The air-testing report shows that concentrations of formaldehyde, particulates (PM10 or PM 2.5, as applicable), ozone (as applicable), total volatile organic compounds (TVOC), target chemicals from CDPH Standard Method v1.1, and carbon monoxide (CO) are within the LEED limits.
Views
78% of the regularly occupied space has access to quality views.